
The principle of operation of the steering rack with electric power. Power steering electrics or hydraulics - choose the best option
September 7, 2016The struggle to improve driving comfort has been going on since its invention. At first, turning the steering wheel was made easier by increasing the size of the steering wheel itself and by introducing a gear transmission. Then hydraulic boosters (GUR) appeared, and recently the drives - assistants became electric (EUR). To understand the difference between them, it is worth studying the principle of operation of the electric power steering.
The principle of operation of the EUR
The electrical assembly, whose task is to facilitate the rotation of the steering wheel, consists of the following elements:
- asynchronous type electric motor;
- a mechanical drive connecting it to the steering mechanism of the car;
- own control unit with sensors.
In small cars, where little effort is required to turn the wheels, a small EUR block is installed under dashboard. In middle-class cars, the electric power steering under the dashboard will no longer fit, and therefore is taken out into engine compartment. In both cases, the electric motor drive is connected to the steering column shaft.
When driving large cars and heavy SUVs, you need to develop more effort to turn the wheels. Therefore, they involve the EUR drive, which works directly with the steering rack. Regardless of the location of the electric motor and its connection to the mechanism, the principle of operation of the electric power steering remains unchanged. It consists in automatic switching on electric drive and transfer of additional force to the mechanism when the driver turns the steering wheel. The amount of torque generated by the amplifier depends on three parameters:
- Angle of rotation. It is measured by a sensor built into steering column.
- Steering wheel effort. It is determined by a special sensor in the form of a twisting torsion bar, which has a mechanical connection with the shaft. The more the torsion bar twists, the more force the engine develops.
- Movement speeds. This information comes from the controller, and he takes it from the speed sensor.
Based on these readings, the electronic unit controls the actuator according to the situation. At low speed, strong twisting of the torsion bar and a large angle of rotation (parking or turning), the amplifier unit produces maximum power. While driving in a straight line, the driver does not need special assistance, therefore the EUR is connected minimally.
About additional functions of electric amplifiers
The electric power steering device is conceived in such a way that, if necessary, the electric motor can turn the wheels of the car both simultaneously with the driver and independently. This gives scope for the implementation of additional functions:
- automatic "steering" to keep the car on a straight path;
- returning the wheels to a straight position after making a maneuver, the EUR can do this when the driver releases the steering wheel after making a turn;
- creating "heaviness" on the steering wheel in different driving modes to make the steering wheel more informative;
- perform automatic parking without driver intervention.
At the same time, the EUR does not interfere with the direct control of the wheels when the engine is turned off or if there is a breakdown, the mechanical connection between them and the steering wheel is maintained.
Pros and cons of the EUR system
Electric boosters during operation develop a weak torque compared to how the hydraulic booster works. Because of this, they are used just on passenger cars , trucks are still equipped with hydraulics. This is the only significant drawback of EUR systems among the many advantages:
- Thanks to the electric drive, such amplifiers are quite reliable and practically do not need maintenance.
- Simplicity. There are no belts, pumps or hydraulic fluids.
- Reducing gasoline consumption by up to 200 grams per 100 km compared to the gain from the power steering, since the EUR does not take energy power unit through a belt drive.
- The ability to change the settings and the amount of gain in different driving modes.
Compactness can be added to the advantages of electric amplifiers, because all the elements are located in one block. But even in the event of a breakdown, the entire unit will have to be replaced, which will be expensive.
Cars with electric power steering have long ceased to be something unusual. Even the most conservative motorists tempered their skepticism and recognized the convenience of this knot. Indeed, driving a car equipped with an electric booster is much more comfortable. You quickly get used to it and do not think at all about how this comfort is achieved. And not many people know the principle of operation of the electric power steering and its design. Meanwhile, knowing how the EUR works is necessary not only to improve education, as one of the heroes of the Soviet cartoon said, but also in order to get rid of the biased attitude towards it, which, unfortunately, still exists.
Design
In general, most of the tales about electric power steering are based on a distorted view of the principle of its operation. Indeed, it is difficult for the average car enthusiast to understand how electricity helps to turn the steering wheel. It even seems to some that it is not the steering wheel that rotates, but some kind of joystick, and the electronics turn the wheels.
Meanwhile, the design of the EUR is quite simple to understand. We emphasize that it is for understanding, because technically everything is implemented quite simply. Therefore, we will try to consider the device of the EUR as accessible as possible.
So, the design of the electric power steering, in a form that is clear enough to understand, is shown in the figure. Obviously, the main elements of the ESD are
- Steering angle sensor;
- Steering wheel moment sensor;
- Electric motor;
- EUR control unit.
It should be noted right away that the above drawing, of course, does not claim to be an exact resemblance to the real EUR and serves to better understand the principle of its operation.
The main element of the electric amplifier can be considered an electric motor. It is he who helps, figuratively speaking of course, turn the wheels. Together with the sensors, the electric motor constitutes the so-called servo drive. What it is? In general, there are many definitions of this device, and all of them are quite complex. But, as they say, as a first approximation and in relation to the electric booster, this means that the electric motor is controlled using the steering wheel. More on this later, but for now let's turn to the figure again. It can be seen from it that the gears of the steering shaft and the engine shaft work for one steering rack. Of course, this is shown schematically. On a real electric amplifier, the gears are not located in the same plane at all. Most often in a real design, the electric motor is located on the steering shaft. But the essence of its design does not change from this, in any case, when the steering wheel is turned, the servo drive shaft rotates proportionally. As a result, the driver has to exert less effort to turn the wheels. It's all about the design. Naturally very short and very approximate. But for now it is enough to understand the general principles. Now in more detail about how the electric power steering works.
The principle of operation of the electric power steering
Very often, one of the shortcomings of the EUR is called the low information content of the steering wheel. What does it mean? This means that the steering wheel is very easy to turn and as a result, the driver, as they say, does not feel the road. Such statements do not correspond to the truth, otherwise, why is the electric amplifier literally crammed with electronics. Indeed, the servo does not work with a constant force. The algorithm of its work depends on the specific conditions.
When parking a car, its high maneuverability is important, and not at all the information content of the steering wheel. In this case, the electric motor works with maximum effort, providing the driver with the so-called "light steering" from the extreme left to the extreme right position.
The higher the speed, the less maneuverability is needed. Moreover, sharp turns become simply dangerous. Therefore, the electronics reduce the efficiency of the servo drive and, thus, it practically does not affect the control of the car. As a result, the driver turns the steering wheel with a noticeable effort, and here you have the necessary information content. Thus, the principle of operation of the electric power steering does not imply constant assistance to the driver, but the optimal one, at the moment, based on the analysis of many parameters.
Speaking about the low information content of the EUR, it is sometimes mentioned as a drawback, the need for a forced return of the wheels to the middle position. Those who claim this have either never driven a car with EUR or are using outdated data. All modern electric boosters have an active steering wheel return to its original state. This is also done with the help of a servo. Therefore, it makes sense to consider his work in more detail.
EUR servo drive: principle of operation
The figure shows the EUR electric drive in section. Obviously, the main parts are:
- Synchronous 3-phase electric motor;
- Worm shaft;
- Steering gear;
- Coupling;
- Rotor position sensor.
First, why the EUR motor is synchronous and not collector. It would seem that it is more logical and cheaper to use the second type in a car. Initially, it was. But the principle of operation of the EUR involves the constant switching on and off of the electric motor, which significantly affects the service life of the brush-collector unit. After all, it is at the moment of starting the engine that the maximum current is consumed, which is accompanied by the formation of a powerful spark. As a result, permanent Maintenance or replacement brushes. Therefore, designers had to choose between an asynchronous and a synchronous motor. We settled on the latter, as more simple. But let's go directly to the design of the electric drive.
The shaft of the synchronous motor is connected to worm shaft. The latter, together with the gear, is a worm gear. Thus, torque is transmitted from the EUR electric motor directly to the steering shaft, supplementing the force applied to the steering wheel.
The rotor position sensor is necessary for the normal operation of the synchronous motor. The fact is that the motor starts to rotate if voltage is applied to only two of its three windings. To which control device it is possible to install using the DPR. But the main element of the servo without any exaggeration can be called a force sensor.
Force sensor operation
The principle of operation of the force sensor is based on the design features of the steering shaft. It lies in the fact that the steering shaft is divided into two parts. Most often they are called the input shaft and the output shaft. The shafts are interconnected by means of a torsion bar, as shown in the figure.
What is torsion. Roughly speaking, this is a metal rod made of springy steel. It allows for slight twisting about the vertical axis. And after that it returns to its original position.
So, the input and output shafts of the electric amplifier are interconnected by a torsion bar. Any attempt to turn leads to displacement of the shafts relative to each other. The maximum offset angle is a few degrees to either side. If this limit is exceeded, there will be a hard coupling between the two parts of the shaft, in fact, turning them into one. By the way, it is thanks to the torsion bar, which turns out to be a little twisted when cornering, that there is always a certain effort on the steering wheel that helps the driver feel the road better.
It is the angle of displacement between the input and output shaft that the force sensor measures. A large angle indicates a strong twisting of the torsion bar, that is, a significant effort applied to the steering wheel. This information is transmitted to the electric booster control unit, which outputs a voltage of the appropriate magnitude and polarity to the motor windings.
In addition, the power steering control unit receives data from the speed sensor. Due to this, the operation is adjusted in accordance with the speed of the vehicle. The faster the car moves, the less torque on the motor shaft. And at a speed of more than 75 km / h, the EUR turns off completely, without affecting the control of the car.
Another sensor that affects the operation of the EUR is the crankshaft position sensor. Thanks to him, the electric power steering only works when the engine is running, and not just after the ignition is turned on. This is important, given that the current consumption of the EUR is not much less than 50 Amperes.
How does the electric power steering of a car work? The principle of operation of the electric booster is an electric drive, which gives additional effort when turning the steering wheel. With this structural element, you do not have to turn the steering wheel with both hands. The sensor measures the torque and transmits it to the amplifier control unit. Depending on the angle of rotation, this block calculates the power that needs to be delivered to the amplifier motor. The sensor itself is located in the steering column switch. For feedback, another sensor is located on the engine rotor, it also transmits information about the speed to the control unit.
Electric power steering appeared in the mid-nineties. At the time of 2016, it is on half of all cars on the planet. Such great popularity is due to a number of its characteristics and the almost absence of shortcomings. Its advantages over hydraulic booster are:
- compactness;
- point adjustment of characteristics;
- the amount of information provided to the work;
- reliability and economy;
- little noise.
Only its power can be attributed to the minus, which is why only power steering is still installed on heavy vehicles.
At first glance, such a sophisticated system is useless, but it provides the calculation of the force on the electric motor in the entire range of steering. This effort depends on parameters such as:
- The amount of torque on the steering wheel.
- The speed at which the car is traveling.
- Engine turnover.
- Steering wheel speed.
While in power steering it gives approximately the same effort over the entire range.
Steering schemes
There are 3 schemes for installing an electric amplifier. Regardless of the scheme, the general design of an electromechanical amplifier consists of an electric motor, a mechanical transmission, two sensors and two gears or a parallel drive.
- The EUR is mounted on the steering column. This is the most compact version, in which it does not require much effort to turn the steering wheel. The electric motor itself and the mechanical transmission are placed under the steering wheel. A huge plus is being in the cabin, and not under the hood, here the device is protected from dust and dirt, and this, in turn, prolongs the service life. Also, in the event of a device failure, it will be easy for you to figure out the principle of installation and change it yourself, which will save money. This type of amplifier mount is used mainly in a small class of cars.
- Steering rack installation. This is how the amplifier is installed mainly on minibuses and SUVs. Here, more force is required, which is transmitted through the gear. After all, what more car, the more it weighs and the more effort it takes to turn.
- Installation on a ball screw mechanism, where through a belt drive, the force from the electric motor is transmitted to the rail. This method provides the greatest effort of the electric motor when turning. This is how electric power steering is installed on tractors and buses.
Whatever the mechanism for installing the electric power steering, there are failures in the control unit, if it fails, it does not block the steering wheel. And the car can be safely driven away to the service, where it will be changed or adjusted.
The device and principle of operation of the EUR
How does electric power steering work in terms of safety? The electric power steering is much simpler than the power steering. He doesn't have any Supplies in the form of liquids. There are no many moving joints and seals (critical points for breakage). That is why now there is a massive rejection of old hydraulic boosters. Even domestic VAZ manufacturers have switched to this technology.
Technical characteristics of the electric amplifier:
- supply voltage (nominal) - 12 V;
- maximum compensating moment - 35 Nm;
- maximum consumption current - 50 A;
- current consumption (the force on the steering wheel is applied, the output shaft of the amplifier is blocked) - no more than 15 A.
Its appearance has helped automakers implement a number of new features, such as:
- promotion exchange rate stability;
- automatic parking;
- observance of traffic lanes.
The main modes of operation of the power steering
As you might guess, the power steering does not work all the time. But only when turning the wheels and not at high speeds. However, the wheels turn under different conditions. Accordingly, the work performed by the engine varies from conditions. Modern control units are able to determine in which mode the car is moving and adjust the engine torque to suit them.
Parking mode
When parking, the speed of the car is small or absent at all, and the turning angles by which we turn the steering wheel are large. The information transmitted from the steering angle sensor is sent to the control unit, and if the speed is minimal, and the steering angles and torque are large, then the parking mode is activated. In it, the maximum load is laid down by the electric amplifier. This ensures the so-called "light steering".
City driving mode
City driving is driven by constant stops, turns and lane changes. Here the movement occurs at a speed of 40-60 km / h. As a result, efforts occur in the middle range, the unit processes information about the speed and angle of rotation and gives a signal to the electric motor.
Driving mode on the track
The peculiarity of this ride is high speeds and a small turning angle when changing lanes. Accordingly, a decision is made about a small effort of the engine or its complete absence.
After all, if you do not remove the help in time, the car will turn sharply at the slightest turn of the steering wheel, even at a small angle, which will lead to an accident.
Holding the middle position of the wheels
The control unit often performs the function of holding the middle position of the wheels. This is necessary in conditions of different tire pressures, all information is processed and corrected. Also, when turning the steering wheel in motion, a traction force is added to the circumferential force, which acts on the wheels and changes their position. The control unit takes this into account and adjusts the position.
Breakdown of the electric amplifier
In the event of a breakdown, an error signal is triggered, a light bulb that notifies the driver that something is wrong. This may be a malfunction signal or a warning of protection systems. When the steering wheel is held in extreme positions for a long time, the winding heats up, and the protection turns off the electric booster in order to avoid breakage. This is a sin for drivers who love to park in the wrong place and turn the steering wheel to the extreme position so that their cars cannot be evacuated.
Another common cause of failure is the failure of the speed sensor. It will only help complete replacement him to a new one.
In some cases, it is worth calibrating the electric power steering:
- wheel alignment;
- transition to new disks;
- replacement of spare parts for the EUR or the EUR itself.
The adjustment will allow you to level the steering wheel in the zero position, without deviations to the sides.
Outcome
As a result, we see that the electric power steering comes to replace the hydraulic booster. If at first the electric amplifier was installed only on small cars, now they have reached SUVs and sports cars. Heavy equipment still remains on the hydraulic booster, but even here they put combined options from two amplifiers. Yes, low power makes it difficult to completely replace the hydraulic booster, but all its advantages outweigh a couple of disadvantages.
Electric power steering (common name - electric power steering) is called a structural element of the steering of a car, in which an additional force when turning the steering wheel is created using an electric drive. In design modern car electric power steering is gradually replacing power steering. By 2016 every second a car will be equipped with power steering.
The main advantages of electric power steering compared to power steering are:
- ease of regulation of steering characteristics;
- high information content of the steering;
- high reliability due to the absence of a hydraulic system;
- fuel efficiency, due to the economical use of energy (reduction of fuel consumption up to 0.5 liters per 100 km).
Electric power steering has opened up wide opportunities for creating various systems active safety: directional stability , automatic parking , emergency steering , lane keeping assistance .
There are two main layout schemes for electric power steering:
- the force of the electric motor is transmitted to the steering wheel shaft;
- the force of the electric motor is transmitted to the steering rack.
The most demanded electric booster with a drive to the steering rack. Its other name is electromechanical power steering. Known designs for such a power steering are a dual gear power steering and a parallel power steering power steering.
The electromechanical power steering consists of an electric motor, a mechanical transmission and a control system.
The electric power steering is combined with the steering mechanism in one unit. In the design of the amplifier, as a rule, an asynchronous electric motor is used.
mechanical transmission provides transmission of torque from the electric motor to the steering rack. In an electric power steering with two gears, one gear transmits torque to the steering rack from the steering wheel, the other from the power steering motor. To do this, the rack has two sections of teeth, one of which serves as a drive for the amplifier.
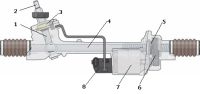
In an electric power steering with a parallel drive, the force from the electric motor is transmitted to the steering rack using a belt drive and a special ball screw mechanism.
The electric power steering control system includes input sensors, an electronic control unit and an actuator.
Input sensors include a steering wheel angle sensor and a steering wheel torque sensor. The power steering control system also uses information from the ABS control unit (vehicle speed sensor) and the engine control unit (speed sensor). crankshaft engine).
The electronic control unit processes the sensor signals. In accordance with the programmed program, an appropriate control action is generated on the actuator - the amplifier motor.
The electric power steering ensures the steering of the car in the following modes:
- turning the car under normal conditions;
- turning the car at low speed;
- turning the car at high speed;
- active return of the wheels to the middle position;
- maintaining the middle position of the wheels.
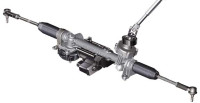
Turning the car is carried out by turning the steering wheel. The torque from the steering wheel is transmitted through the torsion bar to the steering gear. Torsion bar twist is measured with a torque sensor, steering angle is measured with a steering wheel angle sensor. Information from sensors, as well as information about vehicle speed, engine speed, are transmitted to the electronic control unit.
The control unit calculates the required torque of the amplifier motor and, by changing the current strength, provides it to the motor. The torque from the electric motor is transmitted to the steering rack and then, through the steering rods, to the drive wheels.
Thus, the rotation of the wheels of the car is carried out by combining the forces transmitted from the steering wheel and the electric motor of the amplifier.
Turning the car at low speed is usually done when parking. It is characterized by large steering angles. The electronic control system provides in this case the maximum torque of the electric motor, corresponding to a significant increase in steering (so-called. "easy wheel").
When turning at high speed, opposite electronic system control provides the least torque and minimum steering gain (so-called. "heavy wheel").
The control system can increase the reactive force that occurs when turning the wheels. There is a so-called. active return of the wheels to the middle position.
When operating a car, there is often a need to maintain the average position of the wheels (driving with a side wind, different tire pressures). In this case, the control system provides correction of the average position of the steered wheels.
The electric power steering control program provides compensation for front-wheel drive vehicle drift caused by different lengths of drive shafts.
In a number of active safety systems, the electric booster functions without the participation of the driver. In the stability control system, it provides reverse steering of the wheels, and in the parking autopilot - automatic parallel and perpendicular parking.
Ease of driving is a very important factor in ensuring traffic safety. Throughout the history of the automotive industry, engineers have worked on this daunting task. And if the principle of operation has remained unchanged and is the transfer of the rotational force of the steering wheel to the front wheels of the car using a rack and pinion steering mechanism, then the technique for implementing this principle has changed significantly. The latest achievement in this area is the electric power steering.
If it is already a well-known device and has been used by car manufacturers for more than a dozen years, then the EUR is relatively young. Consider the principle of operation of the electric power steering.
Let's start with the EUR device. It consists of an electric motor, a mechanical gear train, a steering angle sensor, a steering torque sensor and a control unit. Also, the control unit receives data on the speed of the machine (from ABS systems) and about the crankshaft speed (engine speed). Based on all these data, the control unit calculates the required value and polarity of the voltage supplied to the electric motor. The electric motor, in turn, through a mechanical gear transmission (servo mechanism) creates an additional force that facilitates the control of the front wheels. This force can be applied both to the steering shaft and directly to the steering rack. The specific device of the EUR also largely depends on the class of the machine.
In cars of a small class, where it is not necessary to apply great efforts to the steering wheel, it is small and is installed directly on the steering column. At the same time, being practically in the car interior, it is protected from dust, dirt and moisture, which has a positive effect on the service life of this device. In a middle-class car, a different placement is used - directly on the steering rack, which is affected by the gear, creating additional auxiliary force.
Cars of the minibus and SUV class, due to their high weight, require significant additional effort. Therefore, their device is somewhat different. This is basically a parallel axis design using a toothed belt drive and a “screw-nut on circulating balls” mechanism. And, of course, in the event of a breakdown of the EUR, the controllability of the car will remain. It will only make it much harder to do so.
Main Modes
The electric power steering has two main modes. They are characterized by the speed of the car. In the first mode, when driving at low speed, for example, during parking, when greater maneuverability is needed and the steering wheel has to be turned to the extreme positions either to the left or to the right, the EUR applies maximum force to the steering mechanism, providing "light steering". In this mode, you can turn the steering wheel with one finger.
On the contrary, when driving at high speeds, the steering becomes “hard”, creating the effect of returning the wheels to the middle position. This was done to improve traffic safety.
There are also modes for keeping the car on the road with a strong side wind, when driving on wheels, which has a different degree of pumping. These modes are achieved through special settings of the control unit. On business and premium class cars, the presence of the EUR allows you to implement the option automatic parking.
Advantages of EUR
From an economic point of view, the main advantage of the EUR is that the use of an electric motor eliminates the need to take part of the power from the car engine.
This allows you to save at least half a liter of fuel per hundred kilometers, unlike a car with power steering. An important advantage is the reliability of this system. There is no need to constantly check the belt and power steering fluid level. The electric power steering is more informative and provides a better connection between the driver and the road. The presence of additional modes makes driving more comfortable. Unlike cars with power steering, the wheels can be held in extreme positions indefinitely.
And, of course, the compactness of the device is also one of the advantages of the EUR over other systems.
Disadvantages of EUR
At the moment, it is not yet possible to use the EUR on heavy trucks requiring a lot of effort when turning the steering wheel. For them, power steering remains the only and reliable option.
Another thing to note is the fear of moisture. Water and condensation can destroy fuses and the motor. The disadvantages include the still high cost of this system. At the same time, it is becoming more and more popular and widespread.
Video "What is EUR"
After watching the video, you will find out what the EUR is and what its pros and cons are.